Technology alone doesn’t make our products—our challenger spirit and uncompromising craft do. We strive to put the soul into every lens and camera by questioning conventions and perfecting innovation. Our high-performing lenses and cameras are proof of that.
This progressive spirit is embodied in our engineers’ exploration of new technologies and our skilled workers’ relentless refinement of the final product. They collaborate across departments, transforming ideas into reality through the synergy of their diverse skills and technologies.
Making a Sigma product is not a rigid, standardized process—it’s dynamic, requiring constant creativity and dialogue. And when the technology for an idea doesn’t exist, we invent it.
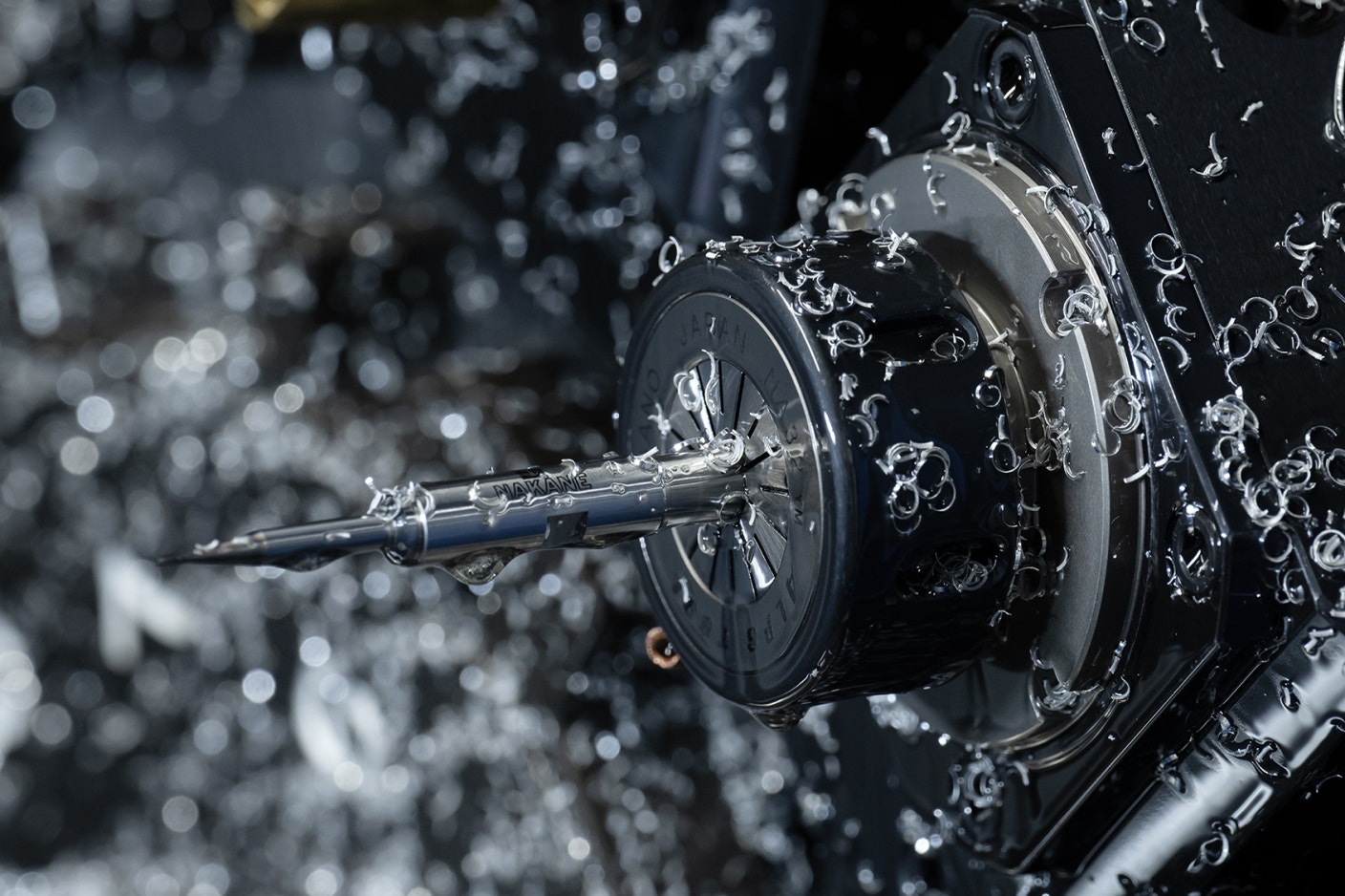
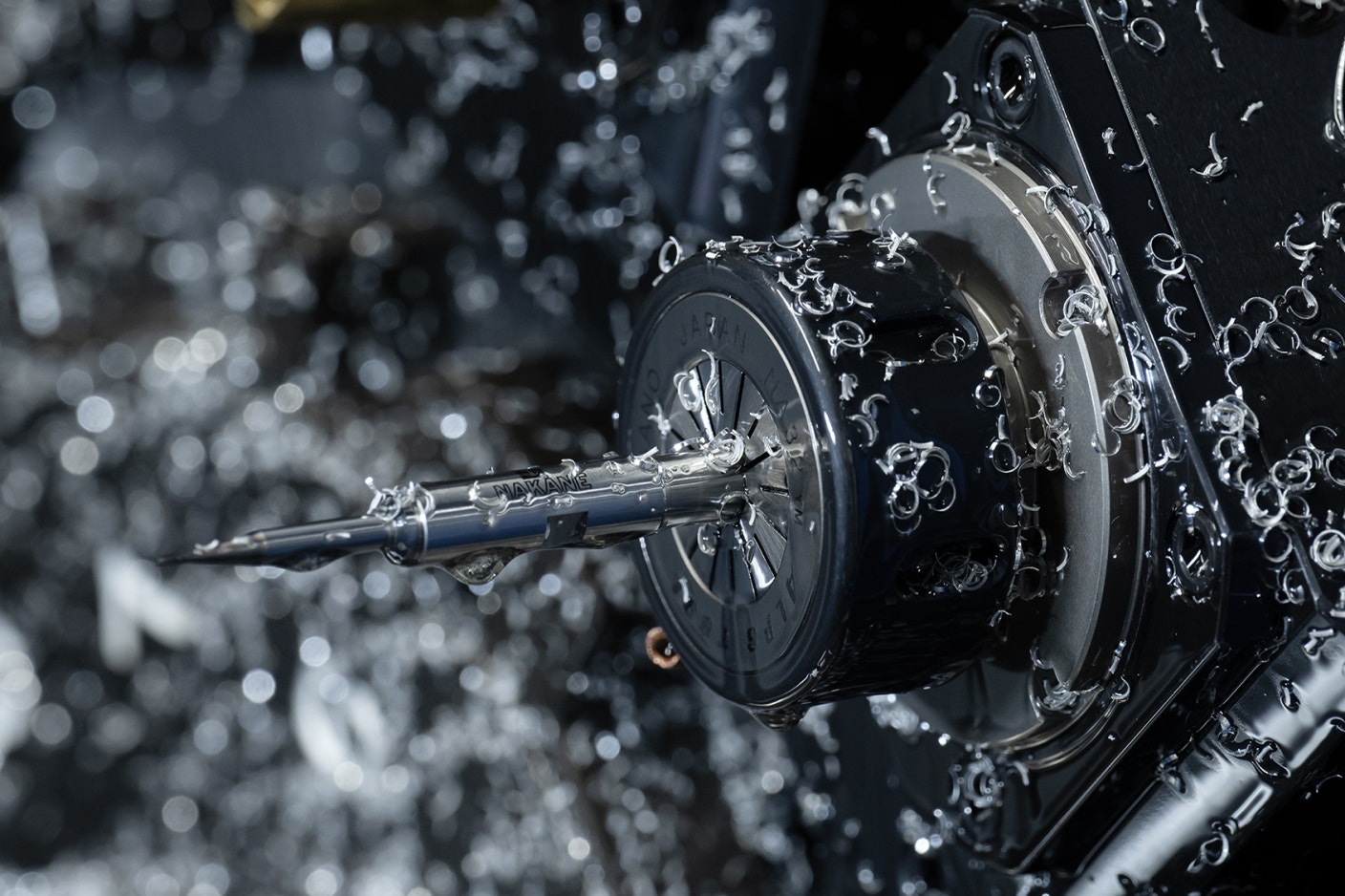
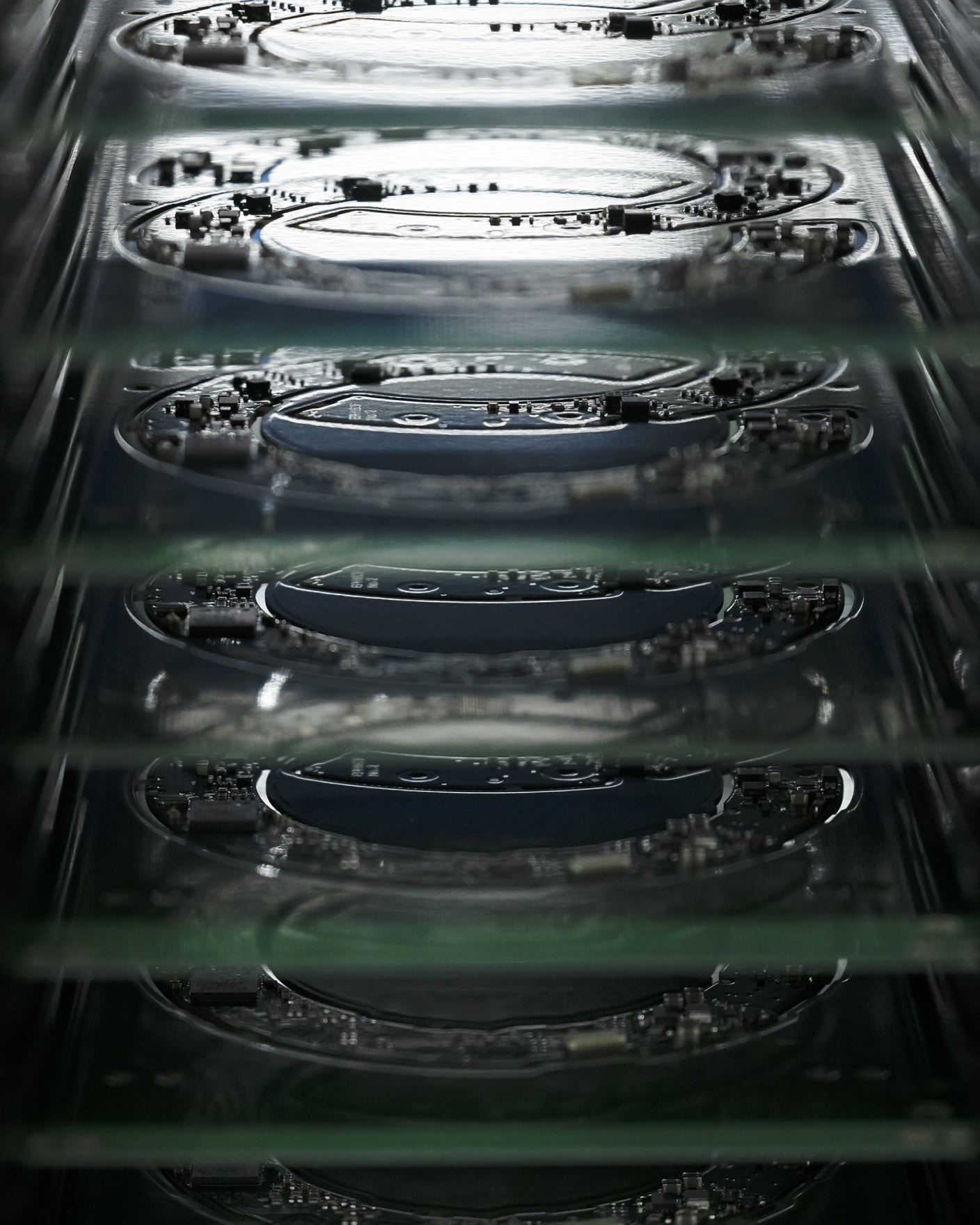
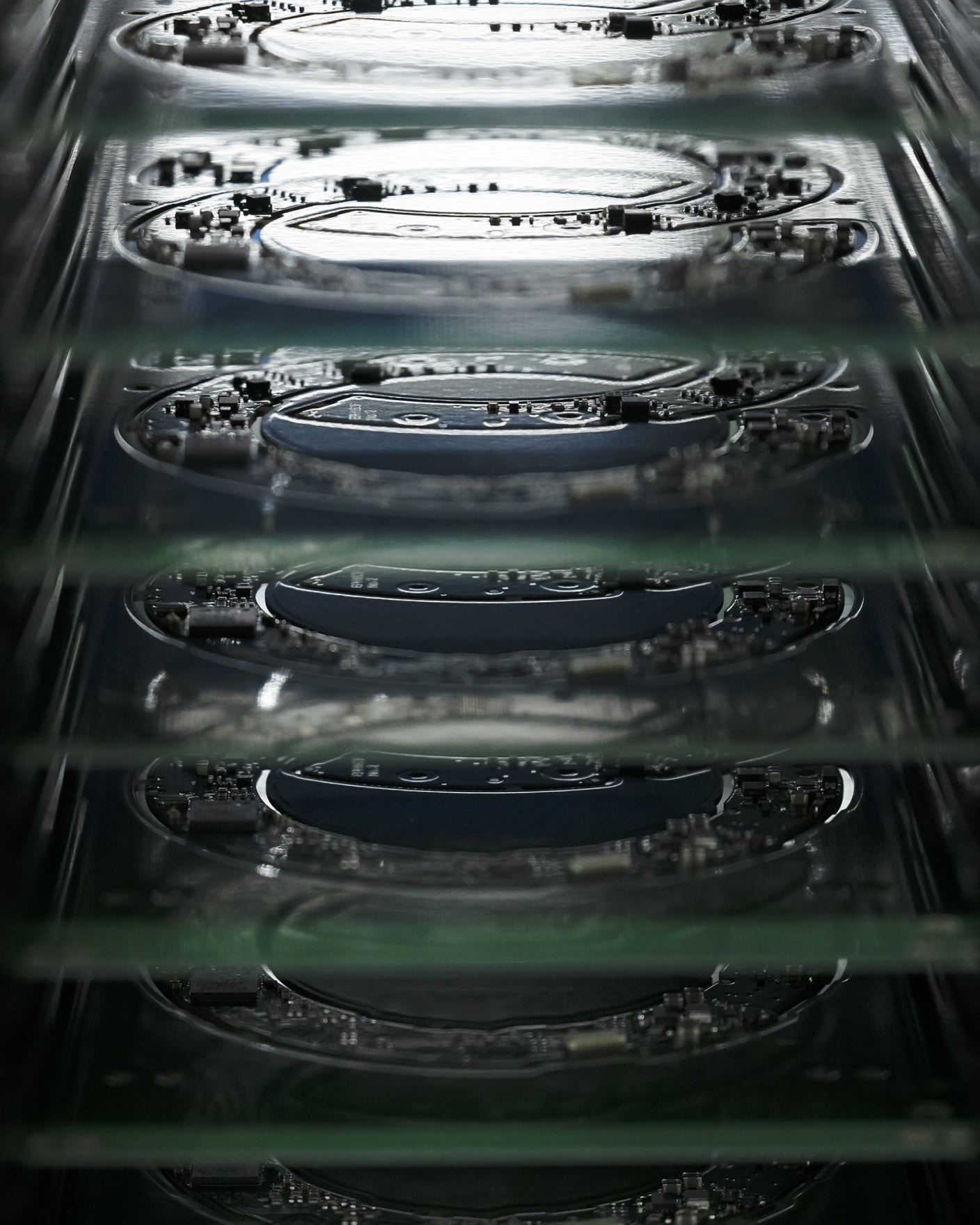
BEYOND DISCIPLINES
Sigma focuses on three key areas: development, manufacturing, and services. Together, they form the foundation of our offering. We design and develop our products at our headquarters and Aizu factory, then bring them to life at our factory. Our services, including our unique lens repair service, reflect the attention to detail that define our development and production.
Sigma’s product development is rooted in the interaction of knowledge and technology. By exchanging thoughts, ideas, and innovations across departments, we continuously gather valuable insights. These insights drive the creation of new ideas and solutions, culminating in our products.
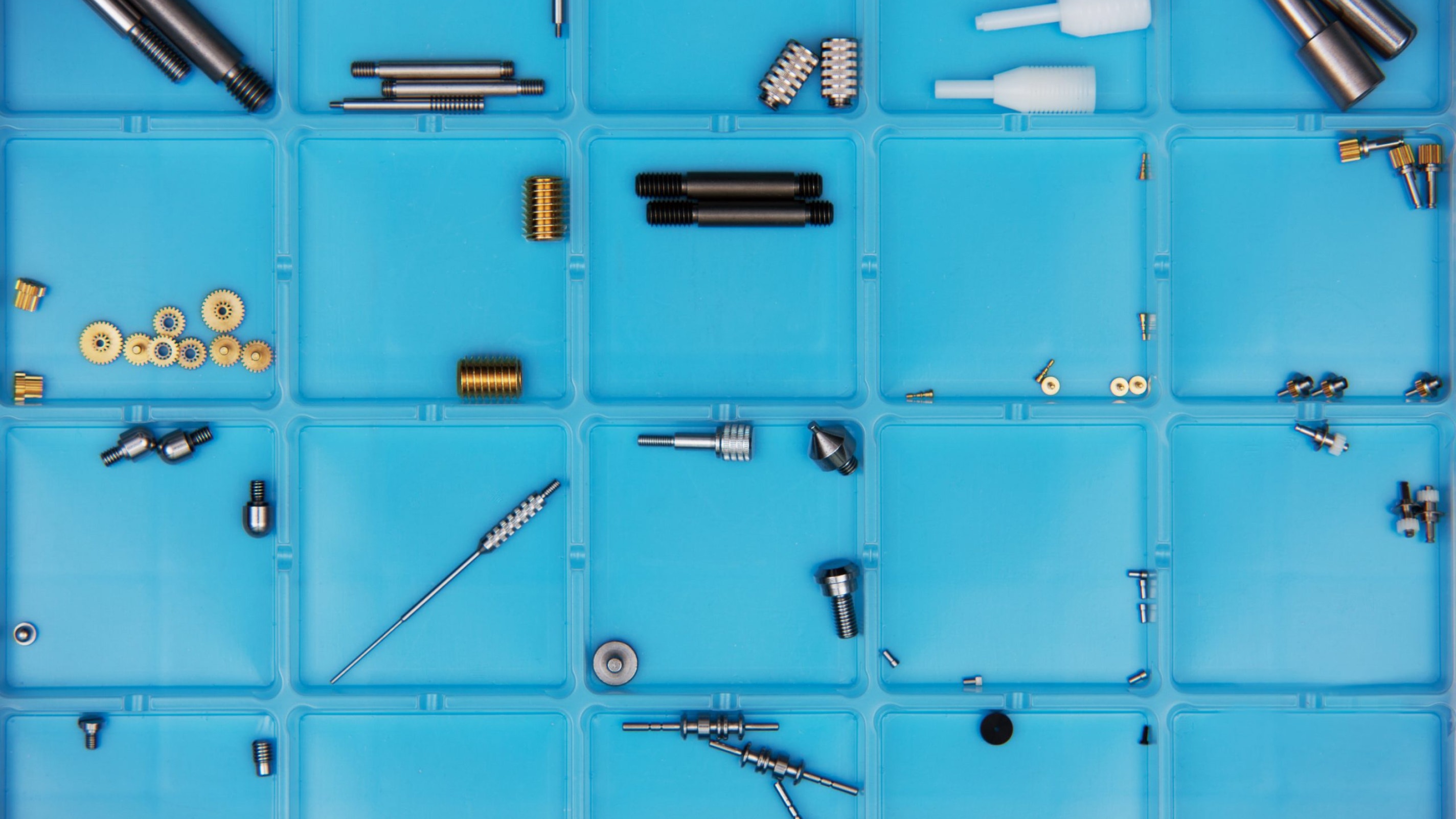
SMALL OFFICE, BIG FACTORY
One fundamental principle at Sigma is "small office, big factory". This phrase captures the balance of creativity and technology that defines our unique production system.
Our office sparks ideas, and our factory turns them into high-quality products. The process can move quickly, beginning with concepts for lenses we want to create or innovations we believe could push photographers' creativity in new directions. Once we’ve figured out how to prototype them, we bring them to life using our advanced manufacturing technology in Aizu.
Our approach requires the integration of human thought and technology, and this balance is integral to our philosophy. Over the years, the interaction between humans and machines has become increasingly refined, thanks to our production, research, development, and assembly being concentrated in the same country for decades.
STAYING VERTICAL
AN INTEGRATED SUPPLY CHAIN
Sigma’s production system has been entirely based in Japan since our founding in 1961. Unlike most production chains in today’s globalized world, we produce and tailor all components either at our own factory in Aizu or in collaboration with local businesses concentrated in the Tohoku region. The Aizu factory started operating in 1973.
Our one-region production system provides other competitive advantages. Direct, face-to-face communication ensures speedy and meticulous product development. And since the same people are consistently involved in our manufacturing processes, they gain more experience, knowledge, and know-how, from which new innovations can spring.
These qualities require a holistic, intangible understanding. We consider them an irreplaceable asset. That is why our domestic, fully integrated production system is so important to us.
THE ULTIMATE IN PERFORMANCE:
OUR LENSES AND CAMERAS
The heart of Sigma is our lenses and cameras.
We strive to surpass expectations in quality when creating our lenses, with the goal of empowering creative ambitions. Our cameras are developed to offer value like no other.
Making photographic lenses is an art. Interchangeable lenses must meet the ever-evolving demands of digital cameras, keeping pace with advancements in resolution and multi-functionality to deliver the highest performance. Our innovation in lens design is grounded in optical expertise, supported by next-generation technology, software development, and mechanical design—all seamlessly integrated. At every step, technical know-how and the experience of skilled engineers are indispensable.
Cameras are another cornerstone of our expertise, and we don’t hold back on innovation here either. Unique products like the Quattro series, the compact, lightweight full-frame fp series, and the BF camera have consolidated Sigma's reputation as a benchmark for cutting-edge development. For instance, the Quattro series features the Foveon sensor—the only sensor in the world with vertical color separation.
Last but not least, designing and manufacturing lenses and cameras—the two fundamental tools of photography—allows us to continually reconsider and redefine the joy and pleasure of taking pictures from the photographer’s perspective. Here, our art of engineering embodies Sigma’s deepest purpose: to engineer for the sake of art.
Introduction
We are driven by a passion for achieving the highest possible quality in optics. As devoted photography enthusiasts, we share a heartfelt connection with dedicated photographers and a deep appreciation for their expressive ambitions.
S
Discover below examples that showcase our uncompromising commitment to quality.1. “Like water through a river”
This was the standard set by Michihiro Yamaki, Sigma’s original founder, for the production process. He often uttered these words during his visits to the factory in Aizu, ensuring that all operations flowed smoothly, like water through a river.
2. 200 different models
Currently, no single unifying mount exists for all interchangeable camera systems on the market. As a result, based on the model numbers of our manufacturing plan, we produce around 200 lens variations at our Aizu factory.
3. High-precision polishing technology
Sigma's spherical lenses are manufactured with an extraordinarily precise surface roughness of just 2 micrometers. Surface roughness refers to the deviation from an ideal, smooth surface. If a lens were scaled up to a diameter of 300 kilometers - the distance between Tokyo and Aizu - the largest bulge would be less than 2 centimeters.
4. From 10mm to 198mm
The largest single lens we produce is the front element of the APO 200-500mm F2.8 EX DG, with a diameter of 198mm. Applying its lens coating takes a meticulous eight hours.
In contrast, the smallest single lens in our lineup is the 7th element of the 8-16mm F4.5-5.6 DC HSM zoom lens, measuring just 10mm.
* As of 20175. Three minutes, three letters
With the introduction of Sigma Global Vision in 2012, we began engraving a three-digit code onto each lens. This code marks the release year of the model. Our hope is that this detail helps customers form a deeper connection with their product by situating it within Sigma’s production history—much like vintage wine.
The three-digit code is engraved using an exceptionally fine end mill. This process is carried out with great care and takes approximately three minutes per lens.
6. Bayonets without compromise
Our brass bayonets are manufactured with thick chrome plating to ensure a quality finish that is resistant to scratches. We adopted trivalent chromium into our production process as soon as it became industrially available. Trivalent chromium perfectly meets our needs for plating without exceeding 0.5 micrometers in thickness. By abandoning the highly toxic hexavalent chromium, we can prioritize the health of our workers and minimize the environmental impact of our factory.
7. "Five more micrometers"
When designing and producing molds, the finishing process is reviewed in thorough detail. For fine adjustments, we commonly work in units of micrometers (0.000001m).
8. Sigma’s proprietary MTF measuring system with data of all shipping lenses
Since the introduction of Sigma Global Vision in 2012, each individual lens shipped has been measured and quality controlled using Sigma's proprietary MTF measuring device. Precise measurement data for every lens is stored at our facility in Aizu.
9. Beyond measuring capabilities
We place great emphasis on the processing technologies used to manufacture molds for parts that demand absolute precision, such as lens cells. With manufacturing deviations never exceeding 0.002mm, the accuracy of the machines at our Aizu factory surpasses even that of state-of-the-art ultrahigh precision 3D measuring devices. We are committed to achieving the highest precision at every step of the process - beyond the reach of modern measuring capabilities.
10. Tactile perfection
Our quality control department ensures the optimal performance and flawless visual appearance of each product. Additionally, they assess crucial qualities that can’t be easily quantified, such as the smoothness of the zoom and focus rings. Our evaluation standards are incredibly strict—to the extent that products can be rebuilt if "the ring doesn't quite feel right".